OEM Thermal Optical Power Detectors, Unmounted and Mounted
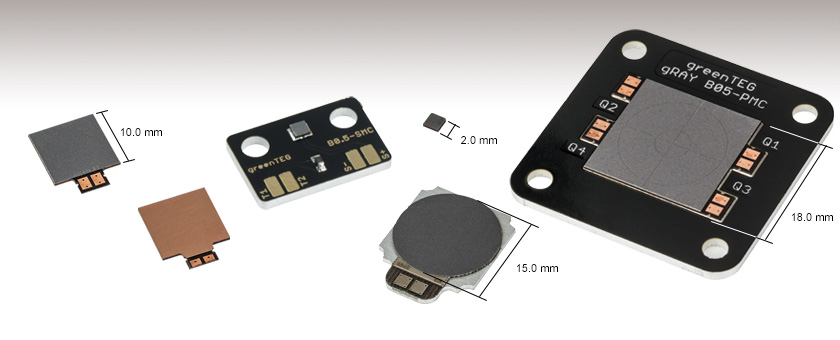
- Surface-Mount-Device (SMD), PCB-Mounted, and Aluminum-Plate-Mounted Options
- Devices have Square or Round Active Areas from 4.0 mm2 to 324 mm2
- Position-Sensitive Devices on PCB or Aluminum Plate
- Ideal for OEM and Custom Systems
TD10X
Unmounted SMD Package
Absorber
on Front
Solderable Copper
on Back
TD15A
Mounted on Aluminum Plate
TD2X
Unmounted SMD
TD2XP
PCB-Mounted TD2X
TD4HR18XP
PCB-Mounted Position Detector
with Four Sensors in Quadrant Configuration

Please Wait
Mounted and Unmounted Detectors |
---|
Unmounted Photodiodes (200 - 2600 nm) |
Calibrated Photodiodes (350 - 1800 nm) |
Mounted Photodiodes (200 - 1800 nm) |
Thermopile Detectors (0.19 - 20 µm) |
Photovoltaic Detectors (2.0 - 10.6 µm) |
Pigtailed Photodiodes (320 - 1000 nm) |
Volume Pricing & OEM Support
Thorlabs is ready to supply these thermal power detectors in high volumes, and we pass the savings associated with planned production on to our customers.
Contact our OEM team to learn more. An OEM specialist will contact you within 24 hours or on the next business day.
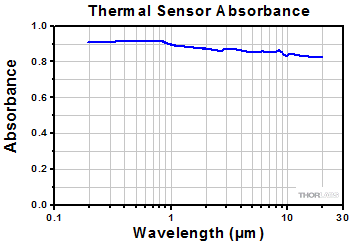
Click to Enlarge
Click Here for Raw Data
These detectors provide uniform absorbance from the UV into the MIR.
Features
- Thermopile-Based Sensors
- Nearly Flat Response from the UV into the MIR
- Unmounted Detectors Have Solderable Copper Back Layer for Mounting
- Sensors Available Mounted to a PCB or Aluminum Plate
- Position Detectors Feature Four Thermally- and Mechanically-Integrated Sensors with Separate Electrical Connections
- Volume Pricing Available
These Thermal Optical Power Detectors include unmounted and mounted single-thermopile sensors, as well as mounted position detectors comprising four individual thermopile sensors that are mechanically integrated into a quadrant configuration. The advantage of these thermal detectors over photodiodes is that the thermal detectors have a spectrally flat response over a broad wavelength range that extends from the UV through the MIR. Additionally, the thermal detectors have negligible dependency on the angle of incidence.
The three unmounted, single-thermopile thermal detectors have sensors optimized for high sensitivity and offer considerable flexibility in both mounting and making electrical connections. All have backing layers of solderable copper that facilitates mounting them on a PCB. Each unmounted sensor is also available mounted on a PCB, which provides mechanical stabilization and convenient copper solder pads for making electrical connections. The TD2XP's PCB has through-contacts and ground layers, while the TD4XP and TD10XP are mounted on metal-core PCBs. All three of these parts include an integrated thermistor.
The TD15A has a sensor that has been designed to accept higher input power levels, which enables its maximum optical power working range to extend up to 50 W. Its Ø15.0 mm sensor is mounted on an aluminum plate to assist with heat dissipation and also includes copper solder pads.
The four thermopile sensors composing the active area of the position detectors are mechanically integrated so that heat from the incident beam flows across the entire active area. As the heat intensity in each quadrant depends on the position of the incident beam, the position of the beam can be determined by comparing the magnitudes of the voltage signals from each quadrant. Position detectors are available mounted on a PCB or an aluminum plate. The sensor of the TD4HR18XP is optimized for high sensitivity and is mounted on a metal-core PCB, while the sensor of the TD4HP18XA is compatible with higher power levels and is mounted on an aluminum plate for enhanced heat dissipation.
Mounting and Handling
As a thermal gradient across the sensor is required to generate the voltage signal, it is crucial that the back side of the thermal detector is mounted to an appropriate heat sink. Active or passive cooling is required to maintain the temperature of the detector's back side at approximately room temperature throughout the measurement. Please see the Handling Instructions manual for more information. This manual also describes proper handling and cleaning methods.
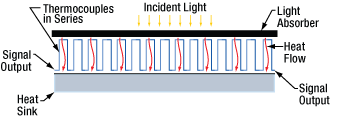
Click to Enlarge
Figure 1: A thermal sensor with axially configured thermocouples, which is depicted as seen from the side. Light is incident on the top, and heat flows down through the thermocouple layer and dissipates in the heat sink below.
Operational Principle
These unmounted and mounted thermal power detectors are based on thermopiles. The top layer of the sensor, which appears gray in color, consists of a light-absorbing material. Located immediately behind the sensor, and in thermal contact with it, is a layer containing multiple thermocouples. Thermocouples are made by bringing two dissimilar metals into contact, and their point of contact is called a junction. The other side of the thermocouple layer must be thermally coupled to a heat sink. The thermocouples are connected in series, and the placement of the junctions alternates from being in close proximity to the absorber to being in close proximity to the heat sink. This axial (or matrix) configuration of thermocouples is diagrammed in Figure 1.
The absorber converts incident light energy into heat. The heat flows from the absorber, across the thermocouples, and to the heat sink, where it dissipates. The temperatures of the thermocouple junctions placed close to the absorber are higher than the adjacent junctions placed close to the heat sink. This arrangement takes advantage of the thermoelectric (Seebeck) effect, in which a temperature difference between adjacent junctions generates a proportional voltage difference. By connecting multiple thermocouples in series, the magnitude of the generated voltage is increased.
Axially-configured sensors, including those used in these unmounted and mounted thermal power detectors, can achieve high resolutions in the microwatt range while providing relatively fast response times. These sensors detect optical powers up to several Watts, which is limited mostly by the thickness of the absorbing material.
Mounting the Detector to a Heat sink
Thermal detectors must be both mechanically stabilized and mounted on an appropriate heat sink, which dissipates heat from the absorbed incident laser light. To ensure sufficient cooling of the detector, choose a heat sink with high thermal conductivity and follow the thermal integration instructions in Chapter 2 of the Handling Instructions manual. Mounting methods include thermally conductive tape, thermally conductive glue, and soldering. After the thermal detector is mechanically stabilized and mounted to its heat sink, electrical connections can be made to the detector.
Unmounted Thermal Detectors
If the thermal detector is unmounted, and the chosen heat sink cannot provide adequate mechanical stabilization, the detector must first be mounted on a substrate that can provide both the necessary mechanical stabilization and good thermal coupling to the heat sink. After the detector is mounted onto the substrate, the substrate should then be mounted onto an appropriate heat sink.
If the chosen heat sink can provide adequate mechanical stabilization, an unmounted thermal detector can be mounted directly onto the heat sink.
Mounted Thermal Detectors
When the thermal detector is mounted on a PCB or other substrate that provides adequate mechanical stabilization but inadequate heat dissipation, the substrate should be mounted onto an appropriate heat sink. This applies to all of these mounted detectors, including the thermal position detectors.
Natural Responses, the Sensor Time Constant, and Power Measurement Predictions
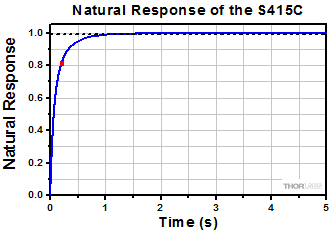
Click to Enlarge
Figure 2: Natural response of the S415C with the dotted line at 99% and the red square indicating the point on the curve corresponding to a single sensor time constant.
The typical natural response of a thermal sensor is its measured response to being instantaneously and steadily illuminated after being held in total darkness. This step function illumination stimulus produces a measured response that can be modeled using an exponential function and is similar to the function describing the rate at which a capacitor charges. Figure 2 shows the natural response measured for our S415C thermal power detector. (The S415C is mounted to a heat sink, calibrated, and includes a C-Series Connector that allows it to be used with our power meter consoles.)
The sensor time constant is defined in terms of how long it takes for the sensor response to reach 99% of its maximum response. The definition used by Thorlabs' power meter consoles is that when the sensor has reached the 99% level, a time period equal to five sensor time constants has elapsed. In Figure 2, the dotted line corresponds to the 99% level and the red square to the response after a single sensor time constant has elapsed. When the sensor's natural response characteristic function is known, it is possible to use it to model and predict the final power reading well before the sensor reading has stabilized.
Protect Thermal Power Sensors from Thermal Disturbances
For the most accurate results, thermal power sensors should be protected from air flow and other thermal disturbances during operation. Otherwise, measurements will drift. This is of particular importance for low power sensors with high resolution. Handheld use is not recommended for any of the thermal power sensors, as body heat transferred to the sensor or heat sink can negatively impact the accuracy of the measurements.
Pulsed Laser Emission: Power and Energy Calculations
Determining whether emission from a pulsed laser is compatible with a device or application can require referencing parameters that are not supplied by the laser's manufacturer. When this is the case, the necessary parameters can typically be calculated from the available information. Calculating peak pulse power, average power, pulse energy, and related parameters can be necessary to achieve desired outcomes including:
- Protecting biological samples from harm.
- Measuring the pulsed laser emission without damaging photodetectors and other sensors.
- Exciting fluorescence and non-linear effects in materials.
Pulsed laser radiation parameters are illustrated in Figure 1 and described in the table. For quick reference, a list of equations is provided below. The document available for download provides this information, as well as an introduction to pulsed laser emission, an overview of relationships among the different parameters, and guidance for applying the calculations.
Equations: |
||||
![]() |
and | ![]() |
||
![]() |
||||
![]() |
||||
![]() |
||||
Peak power and average power calculated from each other: |
||||
![]() |
and | ![]() |
||
Peak power calculated from average power and duty cycle*: | ||||
![]() |
*Duty cycle (![]() |
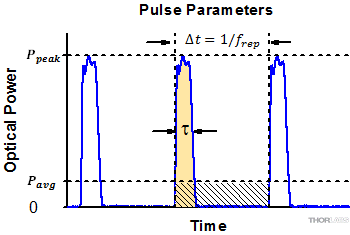
Click to Enlarge
Figure 1: Parameters used to describe pulsed laser emission are indicated in the plot (above) and described in the table (below). Pulse energy (E) is the shaded area under the pulse curve. Pulse energy is, equivalently, the area of the diagonally hashed region.
Parameter | Symbol | Units | Description | ||
---|---|---|---|---|---|
Pulse Energy | E | Joules [J] | A measure of one pulse's total emission, which is the only light emitted by the laser over the entire period. The pulse energy equals the shaded area, which is equivalent to the area covered by diagonal hash marks. | ||
Period | Δt | Seconds [s] | The amount of time between the start of one pulse and the start of the next. | ||
Average Power | Pavg | Watts [W] | The height on the optical power axis, if the energy emitted by the pulse were uniformly spread over the entire period. | ||
Instantaneous Power | P | Watts [W] | The optical power at a single, specific point in time. | ||
Peak Power | Ppeak | Watts [W] | The maximum instantaneous optical power output by the laser. | ||
Pulse Width | ![]() |
Seconds [s] | A measure of the time between the beginning and end of the pulse, typically based on the full width half maximum (FWHM) of the pulse shape. Also called pulse duration. | ||
Repetition Rate | frep | Hertz [Hz] | The frequency with which pulses are emitted. Equal to the reciprocal of the period. |
Example Calculation:
Is it safe to use a detector with a specified maximum peak optical input power of 75 mW to measure the following pulsed laser emission?
- Average Power: 1 mW
- Repetition Rate: 85 MHz
- Pulse Width: 10 fs
The energy per pulse:
seems low, but the peak pulse power is:
It is not safe to use the detector to measure this pulsed laser emission, since the peak power of the pulses is >5 orders of magnitude higher than the detector's maximum peak optical input power.
Posted Comments: | |
SK Lee
 (posted 2024-04-26 14:24:51.563) Hi, I am going to use TD10XP.
It was said that it doesn't require power supply to operate the unit but I can't completely understand how to use it.
There are 4 terminals on PCB. It looks like we use only the 2 lower ones listed as 'Detector Positive/Negative Solder Terminals'. What are the other 2 above, listed as 'NTC terminals'? Is that for reading the resistance directly if needed?
And it is said that we read the voltage across the detector terminals. How can we read voltage from thermistor without providing power to it?
Thanks in advance, hkarpenko
 (posted 2024-04-26 10:18:27.0) Dear customer,
thank you for your feedback.
You are correct, that you don´t need any external power supply to operate the detector. Since it is a thermal sensor, you connect the detector terminals accordingly and can readout the voltage signal. The other two connection ports are for the installed thermistor, to readout the temperature. I will reach out to you directly to discuss this further with you. J. Kim
 (posted 2023-11-09 17:39:28.527) I have a TD10XP and want to know how to wire.
Is it not necessary to supply voltage to TD10XP device?
When I apply 1 W of laser power to active area, the output voltage between S+ and S- will be > 100 mV without any voltage supply. Right?
Please let me know an example drawing how to wire at S+, S-, T1 and T2.
Thanks in advance. hkarpenko
 (posted 2023-11-10 08:34:02.0) Dear customer,
thank you very much for your feedback.
You are correct. A power supply is not needed to operate the thermal detector. You can read out the voltage signal and thermistor using the four copper solder pads. A detailed instruction for operating the device can be found available for download next to the specifications sheet. I will contact you directly to discuss this further with you. Asger P
 (posted 2023-06-16 08:49:12.813) Hello, do you have any data on how absorbance of the detectors depends on AOI of incoming light? hkarpenko
 (posted 2023-06-20 10:20:34.0) Dear Asger, thank you very much for your feedback. During our tests we did observe, that the absorbance is negligible dependent on the angle of incidence. I contact you directly to discuss this further with you. Asger P
 (posted 2023-06-16 08:46:38.053) Hello, do you have any data on how absorbance of the TD15A depends on AOI of light? hkarpenko
 (posted 2023-06-20 10:12:13.0) Dear Asger,
thank you very much for your feedback. During our tests we did observe, that the absorbance is negligible dependent on the angle of incidence. I contact you directly to discuss this further with you. Caleb Niles
 (posted 2022-08-21 19:22:33.177) Hello, what is the temperature accuracy in degrees C? dpossin
 (posted 2022-08-22 10:36:30.0) Dear Caleb,
Thank you for your feedback. The TD10X provides a relative measurement accuracy of +/- 0.2%. However the TD10X is not designed for temperature measurement but for optical power measurement in a wide wavelength range. In case you would like to measure temperature you might have a look at https://www.thorlabs.de/thorproduct.cfm?partnumber=UPTEMP. Manuel Abreu
 (posted 2021-11-22 13:51:22.017) Hi
Quick practical question regarding the temperature calibration of the thermopile:
Is there any sensitivity thermal coefficient to correct the output as function of the temperature accessed via the onboard thermistor ?
Best regards
Manuel wskopalik
 (posted 2021-11-26 06:46:28.0) Dear Manuel,
Thank you very much for your feedback!
Unfortunately, we do not specify such a coefficient. The ambient temperature dependency of thermal detectors is however fairly low. I.e. as long as the ambient temperature is constant, the actual ambient temperature has little effect on the results. If there are however changes in the ambient temperature, it is recommended to make a new zero point measurement to compensate for any changes in the output signal due to the temperature change.
I will contact you directly to provide further assistance. Jussi Raittila
 (posted 2021-03-18 04:18:07.75) Hi, what is the maximum operating temperature ? Or to be more specific, what is the melting temperature of soldering of the components ?
I know already that they work fine up to 140C but during the heat up my wire solderings melted (~180C soldering wire) but the components remained on the board. dpossin
 (posted 2021-03-23 08:27:25.0) Dear Jussi,
Thank you for your feedback. Well a temperature of 110°C should be possible for more than 6 hrs. For a shorter period of time e.g. 1hrs heating up the sensor to 150°C should be possible as well. However we do not recommend to heat the sensor above this temperature since this could lead to permanent damage. Daius Grigaitis
 (posted 2020-05-08 04:53:01.877) Hello,
We have TD4XP sensor!
Where can I get characteristics (tables) of NTC resistor and sensor itself?
Way this information is not available in normal way, by simple and clear datasheet? MKiess
 (posted 2020-05-13 08:34:39.0) This is a response from Michael at Thorlabs. Thank you very much for the inquiry. You can download the spec sheet on our website. Below is the link where you can download the spec sheet:
https://www.thorlabs.de/drawings/4329e36deca11a57-7F49D3E2-A139-27A6-C26F1D02FEEC4859/TD4XP-SpecSheet.pdf.
The sensor without mount is the TD4X. The Spec Sheet for this sensor can be downloaded at the documents of the TD4X. Itay Edry
 (posted 2020-02-27 08:05:17.11) I am interasting with 100W power detector. MKiess
 (posted 2020-03-02 10:10:30.0) This is a response from Michael at Thorlabs. Thank you very much for the inquiry. The TD15A, is the OEM Thermal Optical Power Detector designed for an optical power working range of 1mW - 50W. From this OEM series, this is the one that is suitable for the highest power.
For a light source with an average power of 100W, our S322C is more suitable. It can be used for power up to 200W.
I have contacted you directly to discuss further details. Jialong Chen
 (posted 2019-07-26 10:29:34.857) Hi,
I am Phd student from CUHK, The Chinese University of Hong Kong. We bought one TD10XP and felt comfused about the addition of temperature feedback. Could you provide the datasheet of NTC thermistors of TD10XP, i.e. the R/T characteristics? Thanks a lot!
Best wishes,
Jialong MKiess
 (posted 2019-07-30 06:08:35.0) This is a response from Michael at Thorlabs. Thank you for the inquiry. The temperature sensor is a 10 kΩ, NTC Thermistor. I have sent you the necessary graphs by e-mail. user
 (posted 2018-09-21 09:19:42.33) TD2X mechanical documents fail to download nreusch
 (posted 2018-09-25 11:15:58.0) This is a response from Nicola at Thorlabs. Thank you for making us aware of this. We will fix this immediately. mrtimpovey
 (posted 2018-06-20 10:24:44.987) Do you offer any sample services on these products? Nicola
 (posted 2018-06-21 11:50:00.0) This is a response from Nicola at Thorlabs: Thank you very much for your inquiry. These unmounted thermal detectors are designed for OEM applications and especially for integration in space-limited setups. We look forward to discuss your specific requirements in order to choose the detector that is best suited for your requirements. |

- Each is Also Available Mounted to a PCB (See Below)
- Back Layer of Solderable Copper Facilitates Mounting to PCB
- Operation Requires Mounting to an Appropriate Heat Sink
- Smallest Thermopile Detectors Offered by Thorlabs
The compact sizes of these unmounted thermal detectors makes them particularly suitable for integration into setups where space is constrained. Mechanical and electrical integration methods can be chosen based on the needs of the application, provided that adequate cooling is provided. The bottom layer of solderable copper is convenient for attaching these detectors to a heat sink, and the copper solder pads on the TD4X and TD10X facilitate making electrical connections.

- PCB-Mounted TD2X, TD4X, or TD10X (Available Unmounted Above)
- High Sensitivity for Power Measurements Down to 100 µW
- Integrated Thermistor
- Two Ø3.3 mm Mounting Holes
- High-Power Detector Mounted on Aluminum Plate
- Ø15.0 mm Active Area
- Fast 0.6 s Rise Time
- Four 1.6 mm Radius Quarter-Hole Mounting Points
These mounted thermal detectors include a thermopile-based sensor mounted on either a PCB or aluminum plate. Each includes solder terminals for electrical connections and mechanical features for mounting the devices to a heat sink. Their compact size is a benefit for applications where space is limited. The TD2XP features a high-sensitivity sensor, and it is mounted on a PCB with through-contacts and ground layers. The TD4XP and TD10XP also feature high-sensitivity sensors, and they are mounted on metal-core PCBs. The TD2XP, TD4XP, and TD10XP all include thermistors. The high-power sensor used in the TD15A is compatible with incident optical powers up to 50 W, assuming an appropriate heat sink is used, and the aluminum mounting plate assists with thermal management.

- Active Area Comprises Four Thermally-Coupled Square Sensors in Quadrant Configuration
- Each Sensor is an Electrically Independent Thermopile with Its Own Solder Terminals
- High-Resolution, PCB-Mounted Option Provides 30 µm Spatial Resolution
- High-Power, Aluminum-Plate-Mounted Option
- Optical Power Working Range up to 50 W
- Fast 0.25 s Rise Time
The mechanical integration and electrical separation of the four constituent thermopile-based sensors forms a position sensitive device (PSD); heat is free to flow across the entire active area, but the signal from each quadrant measures the response in only that quadrant's thermopile. When the beam spot of the optical input is contained in one quadrant, the output signal from this quadrant will be higher than the output signals of the other three quadrants. If the beam spot moves across the active area towards the center of the PSD, the signals from the four quadrants will become more similar. The X and Y position of the beam is determined by comparing the signal intensities of all four quadrants.
The TD4HR18P features a high-resolution sensor mounted on a metal-core PCB, which has four Ø3.4 mm mounting holes. The TD4HP18XA's high-power sensor is mounted on an aluminum plate, which assists with thermal management and has four 1.6 mm radius mounting points.
These detectors are used in our Calibrated Thermal Position & Power Sensors.