Broadband Polarizing Beamsplitter Cubes in 16 mm Cage Cubes
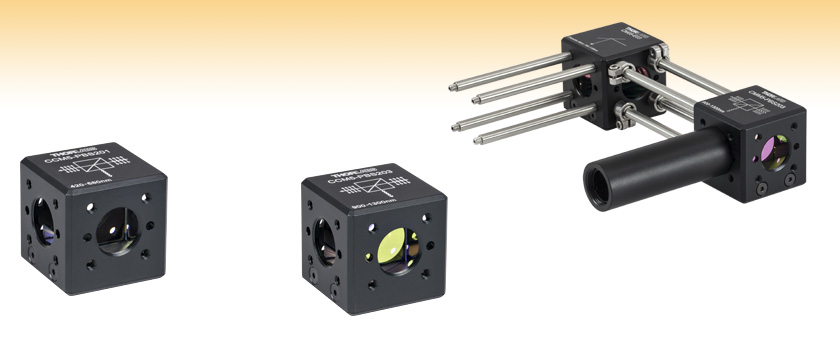
- Transmitted Beam Extinction Ratio: >1000:1
- Reflects S-Polarization by 90°
- SM05 Lens Tube and 16 mm Cage System Compatible
- AR Coated on All Four Optical Faces
CCM5-PBS201
420 - 680 nm
CCM5-PBS203
900 - 1300 nm
Application Idea
CCM5-PBS203 Beamsplitter Cube
Connected in a 16 mm Cage System
with a CM05-E03 Turning Mirror
Cube via Four SRSCA Adapters

Please Wait
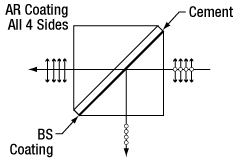
Cube Beamsplitter Diagram
(Coating and Cement Layer Not to Scale)
Features
- 16 mm Cage System and SM05 Lens Tube Compatible Mounts
- Wavelength Ranges Available
- 420 - 680 nm
- 620 - 1000 nm
- 700 - 1300 nm
- 900 - 1300 nm
- 1200 - 1600 nm
- Extinction Ratio
- TP:TS > 1000:1
- RS:RP ~ 100:1
These 16 mm Cage-Compatible Polarizing Beamsplitter Cubes have a dielectric coating along the diagonal interface between the two right angle prisms that make up the cube. This coating reflects s-polarized light, while transmitting p-polarized light. For polarization-insensitive applications, we also offer Non-Polarizing Beamsplitter Cubes, as well as Cube-Mounted Turning Prism Mirrors.
For highest polarization purity, use the transmitted beam, which offers a 1000:1 (TP:TS) extinction ratio. The reflected beam will only have an extinction ratio of roughly 20:1 to 100:1, depending on the beamsplitter. All of the faces of this cube have broadband antireflective coatings that minimize losses due to reflections. The dielectric beamsplitting coating is applied to the hypotenuse of one of the two prisms that make up the cube. Then, cement is used to bind the two prism halves together (refer to the diagram to the right). In order to achieve the desired 50:50 split ratio, the light can enter through any of the faces. One possible orientation is engraved on the top of the cage cube.
A bottom-located 8-32 or M4 tap is included for post mounting. The housings feature four SM05-threaded entrance and exit ports for compatibility with our SM05 (0.535"-40) lens tubes. Four 4-40 tapped holes surrounding each port provide compatibility with our 16 mm cage systems. The Mounted Beamsplitters can be connected to other cage cubes through the use of our cage rods and SRSCA adapters.
For an overview of our complete selection of beamsplitting optics, please see the BS Selection Guide tab. For applications requiring a higher damage threshold, we also offer 1" unmounted High-Power Polarizing Beamsplitting Cubes. These may be mounted in our 30 mm Cage Cubes and incorporated into 16 mm cage systems using our Cage Size Adapters.
Please note that each beamsplitter cube is epoxied within the cage cube mount and cannot be removed.
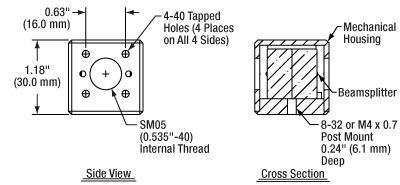
Click to Enlarge
Reference drawing for CCM5-PBS series cubes. The imperial versions have an
8-32 tap, whereas the metric versions have an M4 x 0.7 tap.
Item # Suffix | PBS201(/M) | PBS202(/M) | PBS205(/M) | PBS203(/M) | PBS204(/M) |
---|---|---|---|---|---|
AR Coating Range | 420 - 680 nm | 620 - 1000 nm | 700 - 1300 nm | 900 - 1300 nm | 1200 - 1600 nm |
AR Coating (0° Incident Angle) | Ravg < 0.5% | Ravg < 0.5% | Ravg < 1.0% | Ravg < 0.5% | Ravg < 0.5% |
Ports | 4 Ports with SM05 (0.535"-40) Threading | ||||
Beamsplitter Material | N-SF1 | ||||
Extinction Ratioa | TP:TS > 1000:1 | ||||
Transmission Efficiencyb | TP > 90% | ||||
Reflection Efficiencyb | RS, avg > 95% | ||||
Transmitted Beam Deviationc | 0° ± 5 arcmin | ||||
Reflected Beam Deviationd | 90° ± 20 arcmin | ||||
Clear Aperture | Ø12.50 mm | ||||
Transmitted Wavefront Error | <λ/4 at 633 nm over Ø12.50 mm | ||||
Surface Quality | 40-20 Scratch-Dig |
The shaded regions in the graphs below denote the transmission bands of the beamsplitters for which the performance is guaranteed to meet the stated specifications. Performance outside the shaded regions will vary from lot to lot and is not guaranteed.
Beamsplitter Selection Guide
Thorlabs' portfolio contains many different kinds of beamsplitters, which can split beams by intensity or by polarization. We offer plate and cube beamsplitters, though other form factors exist, including pellicle and birefringent crystal. For an overview of the different types and a comparison of their features and applications, please see our overview. Many of our beamsplitters come in premounted or unmounted variants. Below is a complete listing of our beamsplitter offerings. To explore the available types, wavelength ranges, splitting/extinction ratios, transmission, and available sizes for each beamsplitter category, click More [+] in the appropriate row below.Plate Beamsplitters
Non-Polarizing Plate Beamsplitters |
---|
Polarizing Plate Beamsplitters |
---|
Cube Beamsplitters
Non-Polarizing Cube Beamsplitters |
---|
Polarizing Cube and Polyhedron Beamsplitters |
---|
Pellicle Beamsplitters
Non-Polarizing Pellicle Beamsplitters |
---|
Crystal Beamsplitters
Polarizing Crystal Beamsplitters |
---|
Other
Other Beamsplitters |
---|
Coating Range | Damage Threshold | |
---|---|---|
420 - 680 nm | CWa | 350 W/cm at 532 nm, Ø1.000 mm |
Pulse | 2 J/cm2 at 532 nm, 10 ns, 10 Hz, Ø0.803 mm | |
620 - 1000 nm | CWa | 50 W/cm at 810 nm, Ø0.019 mm |
Pulse | 2 J/cm2 at 810 nm, 10 ns, 10 Hz, Ø0.166 mm | |
900 - 1300 nm | CWa,b | 1000 W/cm at 1070 nm, Ø0.971 mm |
Pulse | 2 J/cm2 at 1064 nm, 10 ns, 10 Hz, Ø0.484 mm | |
1200 - 1600 nm | CWa,b | 1000 W/cm at 1540 nm, Ø1.030 mm |
Pulse | 5 J/cm2 at 1542 nm, 10 ns, 10 Hz, Ø0.181 mm |
Damage Threshold Data for Thorlabs' Polarizing Beamsplitters
The specifications to the right are measured data for Thorlabs' polarizing beamsplitters.
Laser Induced Damage Threshold Tutorial
The following is a general overview of how laser induced damage thresholds are measured and how the values may be utilized in determining the appropriateness of an optic for a given application. When choosing optics, it is important to understand the Laser Induced Damage Threshold (LIDT) of the optics being used. The LIDT for an optic greatly depends on the type of laser you are using. Continuous wave (CW) lasers typically cause damage from thermal effects (absorption either in the coating or in the substrate). Pulsed lasers, on the other hand, often strip electrons from the lattice structure of an optic before causing thermal damage. Note that the guideline presented here assumes room temperature operation and optics in new condition (i.e., within scratch-dig spec, surface free of contamination, etc.). Because dust or other particles on the surface of an optic can cause damage at lower thresholds, we recommend keeping surfaces clean and free of debris. For more information on cleaning optics, please see our Optics Cleaning tutorial.
Testing Method
Thorlabs' LIDT testing is done in compliance with ISO/DIS 11254 and ISO 21254 specifications.
First, a low-power/energy beam is directed to the optic under test. The optic is exposed in 10 locations to this laser beam for 30 seconds (CW) or for a number of pulses (pulse repetition frequency specified). After exposure, the optic is examined by a microscope (~100X magnification) for any visible damage. The number of locations that are damaged at a particular power/energy level is recorded. Next, the power/energy is either increased or decreased and the optic is exposed at 10 new locations. This process is repeated until damage is observed. The damage threshold is then assigned to be the highest power/energy that the optic can withstand without causing damage. A histogram such as that below represents the testing of one BB1-E02 mirror.
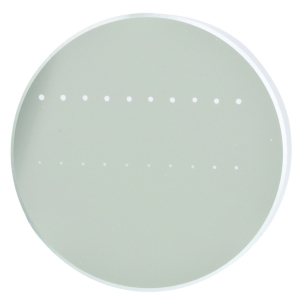
The photograph above is a protected aluminum-coated mirror after LIDT testing. In this particular test, it handled 0.43 J/cm2 (1064 nm, 10 ns pulse, 10 Hz, Ø1.000 mm) before damage.
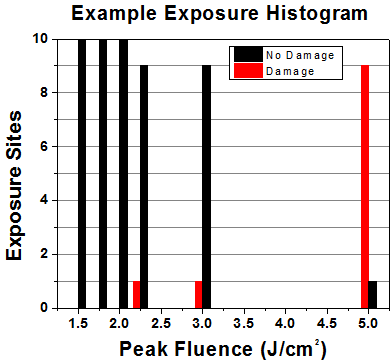
Example Test Data | |||
---|---|---|---|
Fluence | # of Tested Locations | Locations with Damage | Locations Without Damage |
1.50 J/cm2 | 10 | 0 | 10 |
1.75 J/cm2 | 10 | 0 | 10 |
2.00 J/cm2 | 10 | 0 | 10 |
2.25 J/cm2 | 10 | 1 | 9 |
3.00 J/cm2 | 10 | 1 | 9 |
5.00 J/cm2 | 10 | 9 | 1 |
According to the test, the damage threshold of the mirror was 2.00 J/cm2 (532 nm, 10 ns pulse, 10 Hz, Ø0.803 mm). Please keep in mind that these tests are performed on clean optics, as dirt and contamination can significantly lower the damage threshold of a component. While the test results are only representative of one coating run, Thorlabs specifies damage threshold values that account for coating variances.
Continuous Wave and Long-Pulse Lasers
When an optic is damaged by a continuous wave (CW) laser, it is usually due to the melting of the surface as a result of absorbing the laser's energy or damage to the optical coating (antireflection) [1]. Pulsed lasers with pulse lengths longer than 1 µs can be treated as CW lasers for LIDT discussions.
When pulse lengths are between 1 ns and 1 µs, laser-induced damage can occur either because of absorption or a dielectric breakdown (therefore, a user must check both CW and pulsed LIDT). Absorption is either due to an intrinsic property of the optic or due to surface irregularities; thus LIDT values are only valid for optics meeting or exceeding the surface quality specifications given by a manufacturer. While many optics can handle high power CW lasers, cemented (e.g., achromatic doublets) or highly absorptive (e.g., ND filters) optics tend to have lower CW damage thresholds. These lower thresholds are due to absorption or scattering in the cement or metal coating.
LIDT in linear power density vs. pulse length and spot size. For long pulses to CW, linear power density becomes a constant with spot size. This graph was obtained from [1].
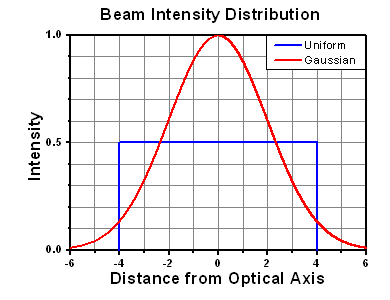
Pulsed lasers with high pulse repetition frequencies (PRF) may behave similarly to CW beams. Unfortunately, this is highly dependent on factors such as absorption and thermal diffusivity, so there is no reliable method for determining when a high PRF laser will damage an optic due to thermal effects. For beams with a high PRF both the average and peak powers must be compared to the equivalent CW power. Additionally, for highly transparent materials, there is little to no drop in the LIDT with increasing PRF.
In order to use the specified CW damage threshold of an optic, it is necessary to know the following:
- Wavelength of your laser
- Beam diameter of your beam (1/e2)
- Approximate intensity profile of your beam (e.g., Gaussian)
- Linear power density of your beam (total power divided by 1/e2 beam diameter)
Thorlabs expresses LIDT for CW lasers as a linear power density measured in W/cm. In this regime, the LIDT given as a linear power density can be applied to any beam diameter; one does not need to compute an adjusted LIDT to adjust for changes in spot size, as demonstrated by the graph to the right. Average linear power density can be calculated using the equation below.
The calculation above assumes a uniform beam intensity profile. You must now consider hotspots in the beam or other non-uniform intensity profiles and roughly calculate a maximum power density. For reference, a Gaussian beam typically has a maximum power density that is twice that of the uniform beam (see lower right).
Now compare the maximum power density to that which is specified as the LIDT for the optic. If the optic was tested at a wavelength other than your operating wavelength, the damage threshold must be scaled appropriately. A good rule of thumb is that the damage threshold has a linear relationship with wavelength such that as you move to shorter wavelengths, the damage threshold decreases (i.e., a LIDT of 10 W/cm at 1310 nm scales to 5 W/cm at 655 nm):
While this rule of thumb provides a general trend, it is not a quantitative analysis of LIDT vs wavelength. In CW applications, for instance, damage scales more strongly with absorption in the coating and substrate, which does not necessarily scale well with wavelength. While the above procedure provides a good rule of thumb for LIDT values, please contact Tech Support if your wavelength is different from the specified LIDT wavelength. If your power density is less than the adjusted LIDT of the optic, then the optic should work for your application.
Please note that we have a buffer built in between the specified damage thresholds online and the tests which we have done, which accommodates variation between batches. Upon request, we can provide individual test information and a testing certificate. The damage analysis will be carried out on a similar optic (customer's optic will not be damaged). Testing may result in additional costs or lead times. Contact Tech Support for more information.
Pulsed Lasers
As previously stated, pulsed lasers typically induce a different type of damage to the optic than CW lasers. Pulsed lasers often do not heat the optic enough to damage it; instead, pulsed lasers produce strong electric fields capable of inducing dielectric breakdown in the material. Unfortunately, it can be very difficult to compare the LIDT specification of an optic to your laser. There are multiple regimes in which a pulsed laser can damage an optic and this is based on the laser's pulse length. The highlighted columns in the table below outline the relevant pulse lengths for our specified LIDT values.
Pulses shorter than 10-9 s cannot be compared to our specified LIDT values with much reliability. In this ultra-short-pulse regime various mechanics, such as multiphoton-avalanche ionization, take over as the predominate damage mechanism [2]. In contrast, pulses between 10-7 s and 10-4 s may cause damage to an optic either because of dielectric breakdown or thermal effects. This means that both CW and pulsed damage thresholds must be compared to the laser beam to determine whether the optic is suitable for your application.
Pulse Duration | t < 10-9 s | 10-9 < t < 10-7 s | 10-7 < t < 10-4 s | t > 10-4 s |
---|---|---|---|---|
Damage Mechanism | Avalanche Ionization | Dielectric Breakdown | Dielectric Breakdown or Thermal | Thermal |
Relevant Damage Specification | No Comparison (See Above) | Pulsed | Pulsed and CW | CW |
When comparing an LIDT specified for a pulsed laser to your laser, it is essential to know the following:
LIDT in energy density vs. pulse length and spot size. For short pulses, energy density becomes a constant with spot size. This graph was obtained from [1].
- Wavelength of your laser
- Energy density of your beam (total energy divided by 1/e2 area)
- Pulse length of your laser
- Pulse repetition frequency (prf) of your laser
- Beam diameter of your laser (1/e2 )
- Approximate intensity profile of your beam (e.g., Gaussian)
The energy density of your beam should be calculated in terms of J/cm2. The graph to the right shows why expressing the LIDT as an energy density provides the best metric for short pulse sources. In this regime, the LIDT given as an energy density can be applied to any beam diameter; one does not need to compute an adjusted LIDT to adjust for changes in spot size. This calculation assumes a uniform beam intensity profile. You must now adjust this energy density to account for hotspots or other nonuniform intensity profiles and roughly calculate a maximum energy density. For reference a Gaussian beam typically has a maximum energy density that is twice that of the 1/e2 beam.
Now compare the maximum energy density to that which is specified as the LIDT for the optic. If the optic was tested at a wavelength other than your operating wavelength, the damage threshold must be scaled appropriately [3]. A good rule of thumb is that the damage threshold has an inverse square root relationship with wavelength such that as you move to shorter wavelengths, the damage threshold decreases (i.e., a LIDT of 1 J/cm2 at 1064 nm scales to 0.7 J/cm2 at 532 nm):
You now have a wavelength-adjusted energy density, which you will use in the following step.
Beam diameter is also important to know when comparing damage thresholds. While the LIDT, when expressed in units of J/cm², scales independently of spot size; large beam sizes are more likely to illuminate a larger number of defects which can lead to greater variances in the LIDT [4]. For data presented here, a <1 mm beam size was used to measure the LIDT. For beams sizes greater than 5 mm, the LIDT (J/cm2) will not scale independently of beam diameter due to the larger size beam exposing more defects.
The pulse length must now be compensated for. The longer the pulse duration, the more energy the optic can handle. For pulse widths between 1 - 100 ns, an approximation is as follows:
Use this formula to calculate the Adjusted LIDT for an optic based on your pulse length. If your maximum energy density is less than this adjusted LIDT maximum energy density, then the optic should be suitable for your application. Keep in mind that this calculation is only used for pulses between 10-9 s and 10-7 s. For pulses between 10-7 s and 10-4 s, the CW LIDT must also be checked before deeming the optic appropriate for your application.
Please note that we have a buffer built in between the specified damage thresholds online and the tests which we have done, which accommodates variation between batches. Upon request, we can provide individual test information and a testing certificate. Contact Tech Support for more information.
[1] R. M. Wood, Optics and Laser Tech. 29, 517 (1998).
[2] Roger M. Wood, Laser-Induced Damage of Optical Materials (Institute of Physics Publishing, Philadelphia, PA, 2003).
[3] C. W. Carr et al., Phys. Rev. Lett. 91, 127402 (2003).
[4] N. Bloembergen, Appl. Opt. 12, 661 (1973).
Posted Comments: | |
Edward Koh
 (posted 2023-10-27 02:23:31.43) Does Thorlabs has a freespace Photodetector that can be affixed at the output of the cube cage? |
Polarizer Selection Guide
Thorlabs offers a diverse range of polarizers, including wire grid, film, calcite, alpha-BBO, rutile, and beamsplitting polarizers. Collectively, our line of wire grid polarizers offers coverage from the visible range to the beginning of the Far-IR range. Our nanoparticle linear film polarizers provide extinction ratios as high as 100 000:1. Alternatively, our other film polarizers offer an affordable solution for polarizing light from the visible to the Near-IR. Next, our beamsplitting polarizers allow for use of the reflected beam, as well as the more completely polarized transmitted beam. Finally, our alpha-BBO (UV), calcite (visible to Near-IR), rutile (Near-IR to Mid-IR), and yttrium orthovanadate (YVO4) (Near-IR to Mid-IR) polarizers each offer an exceptional extinction ratio of 100 000:1 within their respective wavelength ranges.
To explore the available types, wavelength ranges, extinction ratios, transmission, and available sizes for each polarizer category, click More [+] in the appropriate row below.
Wire Grid Polarizers |
---|
Film Polarizers |
---|
Beamsplitting Polarizers |
---|
alpha-BBO Polarizers |
---|
Calcite Polarizers |
---|
Quartz Polarizers |
---|
Magnesium Fluoride Polarizers |
---|
Yttrium Orthovanadate (YVO4) Polarizers |
---|
Rutile Polarizers |
---|